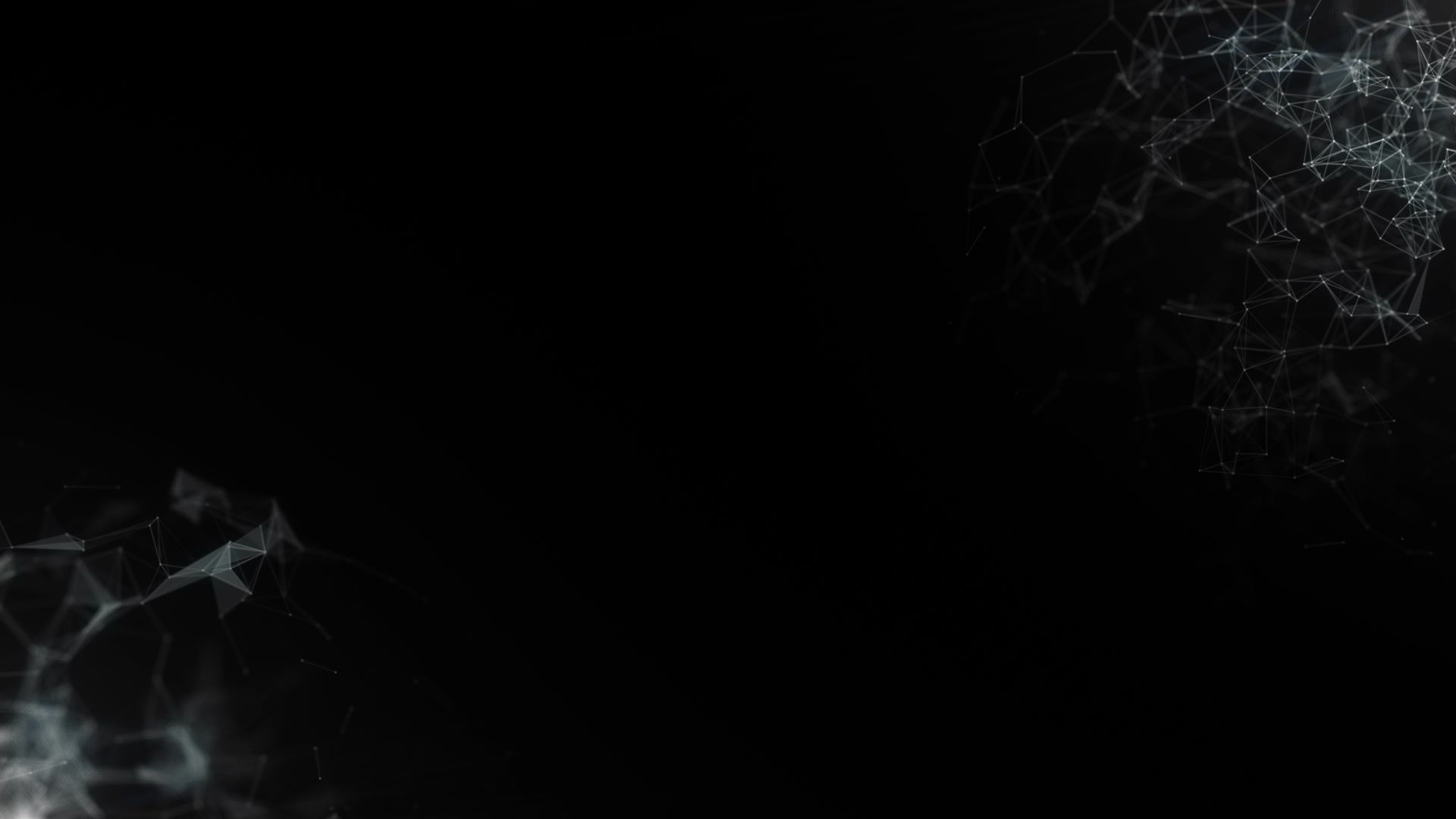
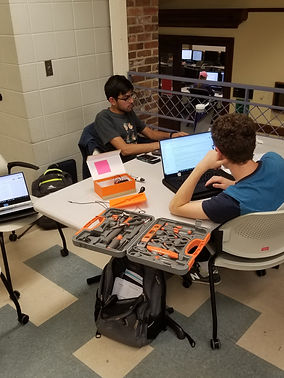

DFM Part 1
It was at this point we started keeping a list of any ideas we came up with for the renovation of the pen. The Product Design Specification, a list of 28 points outlining the details of the product, was then created. This list described the specifications and impacts of our newly manufactured pen. We initially began by considering every idea, regardless of difficulty or length for conception. This list continued to grow alongside the other charts and tables that we created.
Here is the link to the PDS:
After determining the sub-assemblies we wanted to create for the pen, we began to CAD model the pen. We initially created a model of the original pen to serve as a basis for comparison. Then, using the aPriori program, we determined the overall cost of the pen with a variety of factors. We saw that changing the country of manufacturing significantly influenced the overall price of the pen. Additionally, adding greater tolerances for our parts would decrease the cost. This is because the machinery being used does not have to be as precise and a greater variety of differently sized products would still be acceptable as long as the motor functioned. This is an option we kept in case the product cost had become too high for our customers to afford. Our initial aPriori analysis is shown below:
​
​
Now that we had performed a considerable amount of brainstorming and ideation, we then took our ideas and transcribed them into sketches of possible design implementations. We sketched 15 possible ideas, and then from there, chose four of the more promising ideas, and sketched them in further detail.
To accompany our sketches, we designed a Pugh matrix that analyzed the efficacy of our sketches by seeing how each design satisfied our highest customer requirements. Our Pugh Matrix is attached below: